การปรับปรุงกระบวนการทำงานจากเครื่องขึ้นรูป
ส่วนนี้จะแนะนำหลักการและปัญหาที่พบได้ทั่วไปของการใช้แม่พิมพ์สำหรับตัดอันเป็นวิธีการแบบเดิม และข้อได้เปรียบของการเปลี่ยนมาใช้วิธีตัดด้วยเลเซอร์
- วิธีการแบบเดิม: การสร้างแม่พิมพ์สำหรับตัด
- ปัญหาที่พบทั่วไปในการใช้แม่พิมพ์สำหรับตัดแบบเดิม
- ข้อได้เปรียบของการตัดด้วยเลเซอร์
- ใช้ประโยชน์จากความยาวคลื่นเลเซอร์เพื่องานตัดที่มีคุณภาพสูง
วิธีการแบบเดิม: การสร้างแม่พิมพ์สำหรับตัด
หลักพื้นฐานในการตัดโดยใช้แม่พิมพ์สำหรับตัด
วิธีการตัดแบบนี้ จะทำการตัดชิ้นงานโดยอาศัยแรงกดจากด้านบน
ตัวอย่างทางขวาแสดง PCB แบบยืดหยุ่นที่ขึ้นรูปแล้ว พื้นที่ทางเข้าของเนื้อวัสดุหล่อที่วงกลมสีแดงไว้ ตัดโดยใช้แม่พิมพ์สำหรับตัด
แม่พิมพ์สำหรับตัดมีสามประเภททั่วไป
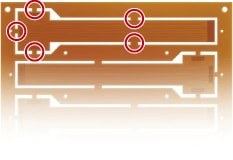
การกดครั้งเดียว (Single-shot stamping)
วิธีนี้จะทำการกดเพียงครั้งเดียวในการตัดชิ้นงานหนึ่งชิ้น
เป็นวิธีการตัดที่เรียบง่ายที่สุด ซึ่งต้องให้คนงานเข้ามายกย้ายชิ้นวัสดุด้วย
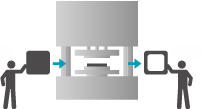
การกดแบบลำดับ (Progressive stamping)
ชิ้นวัสดุจะเคลื่อนที่ตามกันเป็นลำดับผ่านสถานีการตัดสองสามจุด ซึ่งแต่ละสถานีจะใช้แม่พิมพ์สำหรับตัดหนึ่งตัว โดยแม่พิมพ์แต่ละตัวจะมีระยะ Pitch เท่ากัน เครื่องป้อนจะเคลื่อนย้ายชิ้นวัสดุจากสถานีหนึ่งสู่สถานีถัดไป ครั้งละ 1 ระยะ pitch สำหรับทุกๆ รอบการกดแม่พิมพ์
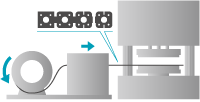
การกดแบบชิ้นงานเคลื่อน (Transfer stamping)
ใช้แม่พิมพ์หลากหลายแบบที่มีรูปร่างแตกต่างกัน และจะถูกจัดเรียงให้กดลงมาพร้อมกันในการกดหนึ่งครั้ง กระบวนการตัดแบบอัตโนมัตินี้จะทำอย่างต่อเนื่องในขณะที่ชิ้นวัสดุเคลื่อนผ่านแม่พิมพ์สำหรับตัด ซึ่งจะต้องมีกลไกการป้อนชิ้นวัสดุที่ทำงานประสานสอดคล้องกัน
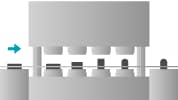
ปัญหาที่พบทั่วไปในการใช้แม่พิมพ์สำหรับตัดแบบเดิม
ปัญหาที่ 1 — การเปลี่ยนขนาดและรูปร่างของชิ้นงานสำหรับตัด
ในวิธีการแบบเดิมคือแม่พิมพ์สำหรับตัด จะต้องใช้แม่พิมพ์ใหม่ทุกครั้งที่รูปร่างของชิ้นงานที่จะตัดนั้นเปลี่ยนแปลงไป ซึ่งส่งผลให้ต้นทุนแม่พิมพ์เพิ่มขึ้นและต้องมีขั้นตอนที่เพิ่มขึ้นสำหรับการเปลี่ยนแปลงในสายการผลิต
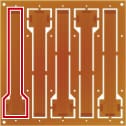
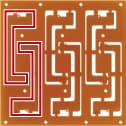
ปัญหาที่ 2 — ชิ้นส่วนต่างๆ ค่อยๆ เสื่อมสภาพลงและเพิ่มงานการบำรุงรักษา
เพราะการตัดต้องใช้แรงกดลงบนคมใบมีดตัด ดังนั้นจึงมีความเสี่ยงที่จะเกิดความเสียหายต่อตัวชิ้นงาน เช่น การโก่งงอของ PCB นอกจากนี้คมใบมีดตัดยังเกิดการสึกได้ ทำให้คุณภาพการตัดลดลงและเพิ่มงานการบำรุงรักษา เช่น การเปลี่ยนทดแทนชิ้นส่วนที่เปลี่ยนได้
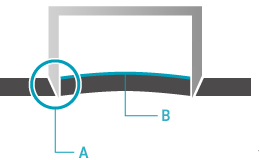
- คุณภาพการตัดลดลงเนื่องจากใบมีดตัดสึกหรอ
- การโก่งงอของ PCB เนื่องจากแรงกดขณะตัด
ข้อได้เปรียบของการตัดด้วยเลเซอร์
หลักพื้นฐานในการตัดโดยใช้เลเซอร์มาร์กเกอร์
วิธีนี้จะทำการตัดหรือเจาะส่วนต่างๆ ของชิ้นงานโดยใช้การปล่อยแสงเลเซอร์แบบไม่สัมผัส
- การกำหนดรูปร่างแบบปรับแต่งเองได้ด้วยซอฟต์แวร์
- การผ่านกระบวนการแบบไม่สัมผัสเพื่อความเสถียรที่มากขึ้น
- ไม่มีชิ้นส่วนที่ต้องเปลี่ยน เพื่อการบำรุงรักษาที่ง่ายขึ้น
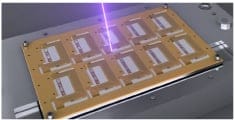
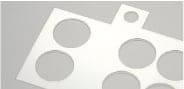
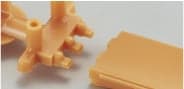
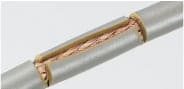


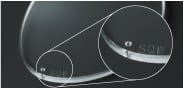
ใช้ประโยชน์จากความยาวคลื่นเลเซอร์เพื่องานตัดที่มีคุณภาพสูง
เมื่อเทียบกับเลเซอร์ความยาวคลื่นมาตรฐานแล้ว โดยทั่วไปเลเซอร์ UV และเลเซอร์สีเขียวจะมีอัตราการดูดซับของวัสดุที่โดดเด่นกว่ามาก ดังนั้นแสงที่ยิงออกมาจะถูกดูดซับโดยพื้นผิวที่จะทำการมาร์กได้อย่างมีประสิทธิภาพ
ซึ่งหมายความว่าไม่จำเป็นต้องเพิ่มพลังงานในงานการตัดคุณภาพสูง
- อัตราการดูดซับสำหรับวัสดุพลาสติกชนิดต่างๆ
- ค่าเหล่านี้มีไว้เพื่อใช้ในการอ้างอิงเท่านั้น และไม่ได้คำนึงถึงการสะท้อนแสงของพื้นผิว
ความสามารถในการระงับผลกระทบจากความร้อนช่วยให้ความเสียหายรอบๆ พื้นที่ตัดลดลง
- Polyimide
-
เลเซอร์ความยาวคลื่นมาตรฐาน เลเซอร์สีเขียว
- PCB
-
เลเซอร์ความยาวคลื่นมาตรฐาน เลเซอร์ UV